FAQ
Aqui você encontra a sua resposta
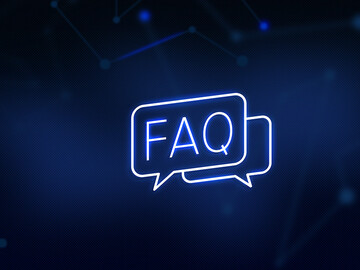
Bem-vindo à nossa página FAQ, na qual você encontra respostas a perguntas frequentes.
Sabemos que às vezes é difícil encontrar a informação correta de forma rápida e simples. Por isso, os nossos especialistas de serviço criaram esta página, para lhe ajudar na solução de problemas e na resposta de perguntas.
Esperamos que você encontre tudo o que você precisa nesta página. Caso você tenha outras perguntas ou necessite de outras informações, não hesite em entrar em contato conosco.
Teste de óleo isolante
Para os sistemas que estão a funcionar, estão disponíveis vários métodos de ensaio para avaliar o estado do óleo isolante. Estes métodos de ensaio podem ser divididos em duas categorias básicas:
- Avaliação do estado atual e da adequação do isolamento em equipamentos eléctricos:
- Medição da tensão de rutura sob carga dieléctrica
- Medição do fator de dissipação
- Análise do envelhecimento do sistema de isolamento:
- Determinação da resistência específica
- Inspeção visual da cor e do aspeto do óleo isolante
O teste de tensão de ruptura dielétrica avalia a capacidade de isolamento dos líquidos isolantes. Com base nos resultados do teste, pode-se determinar se o óleo está envelhecido, devido, por exemplo, ao alto teor de água, impurezas ou oxidação do óleo.
Aqui você encontra todas as informações sobre isso e com quais equipamentos BAUR este teste pode ser realizado.
As seguintes empresas deveriam realizar regularmente um teste de tensão de ruptura dielétrica:
- Empresas fornecedoras de energia, em especialmente em subestações
- Empresas fornecedora de energia, principalmente em centrais elétricas
- Empresas ferroviárias, que utilizam transformadores de alta tensão para locomotivas e instalações de distribuição
- Laboratórios de teste para análises de óleo, que prestam serviços na área de teste
- Fabricantes de transformadores e instalações de distribuição, que realizam controles da qualidade do óleo
- Empresas na área da indústria do óleo, que testam óleo novo durante a fabricação
Atualmente temos cinco diferentes tipos de líquidos isolantes, que são usuais e que você pode testar. Estes abrangem:
- Óleo mineral
- Hidrocarbonetos de alto peso molecular (HMWH)
- Fluidos de silicone
- Líquidos à base de ésteres sintéticos
- Líquidos à base de ésteres naturais (óleo vegetal)
Nas diretrizes IEC 60422 (Diretrizes para o monitoramento e manutenção), VDE 0370 (Diretrizes para o monitoramento e manutenção), bem como de alguns fabricantes de óleo isolante, são recomendados determinados parâmetros).
O ensaio de tensão de rutura dieléctrica é um método comparativamente rápido e simples para determinar o grau de contaminação do óleo isolante. Estes contaminantes são normalmente constituídos por água, mas também podem incluir partículas condutoras, sujidade, depósitos, partículas isolantes e subprodutos da oxidação e envelhecimento do óleo. Para equipamento operacional, o ensaio de tensão de rutura dieléctrica é uma forma prática e eficaz de detetar humidade e outros contaminantes no óleo antes que possam causar uma falha catastrófica. Os conhecimentos adquiridos com este ensaio podem também ser utilizados como auxiliares:
- Previsão da vida útil restante de um transformador
- Aumento da segurança operacional
- Prevenção de incêndios no sistema
- Manutenção de fiabilidade
Os manuais para o monitoramento de óleo isolante em situações operacionais você encontra nas normas IEC 60422 (Diretrizes para o monitoramento e manutenção) bem como VDE 0370 (Diretrizes para o monitoramento e manutenção). Aqui ocorre uma distinção baseada no tipo de transformador, na potência e na carga. Estas normas lhe oferecem diretrizes no que se refere à frequência dos testes que, em caso de resultados desfavoráveis ou esforço especialmente elevado, devem ser abreviados.
Para que os resultados do teste de óleo isolante sejam significativos, é essencial uma amostragem correta do óleo por pessoal treinado. Aqui estão algumas dicas para ajudá-lo a coletar uma amostra de forma limpa.
As características individuais de um óleo isolante podem também aparecer, em maior ou menor grau, noutros óleos. No entanto, a especialidade reside na combinação destas propriedades. Por exemplo, outros óleos de baixa viscosidade podem ter uma tensão de rutura elevada, possivelmente uma resistência elevada e um baixo fator de perda dieléctrica, se estiverem limpos e secos. Mas estas propriedades podem mudar quando o baixo ponto de fluidez, o elevado ponto de inflamação e a excelente resistência à oxidação entram em ação.
É de salientar que os óleos isolantes convencionais têm esta combinação de propriedades sem a utilização de aditivos. Isto é particularmente importante para a reutilização, pois torna-os ideais para a reciclagem.
Localização de falha em cabo
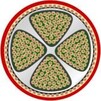
Blindado / multifilar
- Baixa tensão
- 3 ou 4 fases
- Blindagem
- Falhas normalmente entre duas fases
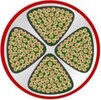
Não-blindado - multifilar
- Baixa tensão
- 3-5 fases
- Falha entre fase-terra e fase-fase
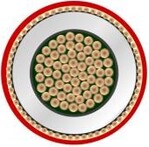
Blindado / Coaxial
- Média ou alta tensão
- 1 fase
- 1 blindagem
- Falha entre fase-blindagem
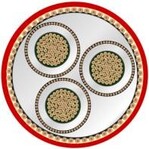
Coaxial blindado
- Média ou alta tensão
- 3 fases
- 3 blindagens
- Falhas entre fase-fase
- Falhas entre fase-fase são pouco prováveis
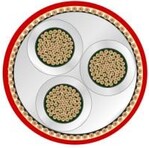
Coaxial blindado
- Média tensão
- 3 fases
- Falhas entre fase-fase ou fase-blindagem
- Localização de falha muitas vezes difícil
De modo geral existem 2 tipos de materiais isolantes para cabos de energia:
- Cabos com isolamento de papel, impregnados com massa (PILC)
- Polietileno reticulado (PEX)
Curto-circuito
Isolações danificadas geram uma conexão de baixa impedância de duas ou mais fases no local da falha.
Falha a terra / curto-circuito a terra
Falhas a terra ou curto-circuitos a terra são ligações de baixa impedância ao potencial de terra. Outro tipo de falha é a dupla falha a terra, que ocorre quando há duas falhas a terra em fases diferentes com pontos de base fisicamente separados.
Falhas no revestimento do cabo
Os danos do revestimento externo de cabo nem sempre levam a falhas diretas. Mas eles podem causar falhas de cabo a longo prazo – entre outros, através da penetração de umidade e de danos de isolação.
Falhas intermitentes
Frequentemente as falhas não ocorrem de forma constante, mas apenas ocasionalmente e em função da carga do cabo. Um motivo disso pode ser o ressecamento de cabos com isolamento a óleo e pouca carga. Outro motivo é a descarga parcial através do envelhecimento ou por "Arborescências elétricas" em cabos.
Interrupções de cabos
Danos mecânicos e movimentos do solo podem gerar interrupções de um ou mais condutores.
O método de reflexão de impulsos (também chamado de TDR) é usado para a localização de falhas de baixa impedância, rupturas do cabo e para a determinação do comprimento do cabo. Saiba mais aqui.
-
Método de medição reflexão de impulsos (TDR) para falhas de baixa impedância e rupturas do cabo
-
Método de impulso secundário/múltiplo SIM/MIM para falhas de alta impedância e falhas de ruptura dielétrica
-
DC-SIM/MIM para falhas intermitentes
-
Condicionamento SIM/MIM para falhas de difícil localização e falhas de cabo úmidas
-
Método de decaimento (Decay) para falhas de ruptura dielétrica com alta tensão
-
Método de corrente de impulso (ICM) para falhas de alta impedância e falhas de ruptura dielétrica
-
DC-ICM para falhas de ruptura dielétrica carregáveis
-
Modo de medição com representação de curvas envolventes para pequenas falhas intermitentes
-
Condicionamento de falha (queima) para falhas de alta impedância em cabos com revestimento de papel e chumbo
Na nossa página de aplicação você pode conhecer os detalhes dos principais métodos de medição.
O método de impulso secundário/múltiplo é o método de pré-localização de falha de cabo de maior comprovação e precisão. Falhas de alta impedância e de ruptura dielétrica são acionadas através de um único pulso de AT, e a distância da falha é medida de forma exata diversas vezes com a técnica TDR e avaliada automaticamente.
Saiba mais aqui.
Com o método de corrente de impulso você pode localizar falhas de alta impedância e de ruptura dielétrica. A distância da falha é determinada através da avaliação dos diagramas de corrente de impulso. Especialmente apropriado para a aplicação em cabos longos. Todos os detalhes para este método de pré-localização de falha em cabo você encontra na nossa página de aplicação.
No DC-SIM/MIM a energia é conduzida diretamente ao cabo pelo gerador de tensão de pulso, a descarga e o arco voltaico no local da falha ocorrem quando o nível de tensão de saída atinge o nível de tensão de ruptura dielétrica almejado.
O método de decaimento é usado para a localização de falhas de ruptura dielétrica com alta tensão. Para a determinação da distância da falha, as ondas de reflexão de tensão oscilantes são avaliadas automaticamente.
Todos os detalhes sobre isso você encontra aqui.
O método de ponte de medição é usado nos seguintes tipos de falha:
- Falhas de cabo de baixa e alta impedância
- Falhas no revestimento do cabo de baixa e alta impedância
- Falhas de condutor a condutor em cabos não blindados
- Falhas em cabos piloto e linhas de sinal
- Falhas em condutores não blindados contra o terra
Para a localização de falhas de alta impedância e intermitentes em cabos subterrâneos é usado o método acústico, para localizar o local da falha exato. Pulsos emitidos por um gerador de pulso (SSG) permitem que um pulso de tensão percorra o cabo, e os campos magnéticos e acústicos são registrados pelo equipamento de localização de falhas em cabos protrac®.
С помощью трассировки можно локализовать следующие типы повреждений:
- Низкоомные повреждения в многожильных скрученных кабелях
- Повреждения линий управления
- Повреждения низковольтных кабелей
- Повреждения с утечкой на землю
- Выявление кабельных соединений
Calibração
A nossa acreditação permanece eficaz e constante enquanto atendermos os elevados padrões e requisitos da qualidade, que são necessários para a acreditação. O nosso engajamento por excelência e melhoria contínua assegura que mantenhamos a nossa acreditação e que também no futuro possamos lhe oferecer serviços confiáveis e qualitativos.
A nossa acreditação é um sinal do nosso engajamento para máximos padrões da qualidade e a nossa busca contínua por excelência. Com este selo de qualidade queremos dar a você como cliente a certeza de que você está trabalhando com uma empresa profissional e digna de confiança.
Estamos convictos que a nossa acreditação nos apoia em trabalhar continuamente em nossos processos e modos de trabalho, para continuar melhorando os nossos serviços e superar as expectativas dos nossos clientes.
Somos acreditados para a calibração das grandezas de medição de corrente e alta tensão. O escopo exato da acreditação você encontra aqui.
O ajuste é um processo independente e se diferencia da calibração. Enquanto a calibração determina o estado atual do objeto de teste, sem fazer alterações no objeto de teste, o ajuste se refere a adaptações ou alterações permanentes no objeto de teste, para ajustá-lo a uma determinada norma ou valor de referência.
No âmbito da nossa calibração acreditada, somente são realizadas medições para verificar a precisão e correspondência do objeto de teste com os padrões definidos. Quando é necessário um ajuste para ajustar o objeto de teste às especificações necessárias, isto é executado como processo separado e não é parte integrante da calibração propriamente dita.
Caso desejado, ele pode ser realizado mesmo assim no decorrer de uma calibração de fábrica ou acreditada.
Descubra o processo completo da calibração acreditada aqui.
A calibração é um processo importante, no qual comparamos as medições do seu equipamento com aquelas de um instrumento de referência mais exato ou normas. Com isso podemos detectar eventuais falhas no equipamento testado. Em alguns casos também fazemos um ajuste para corrigir eventuais desvios. No entanto, uma calibração bem-sucedida não significa necessariamente que o equipamento seja levado ao desempenho especificado. Trata-se muito mais de assegurar que o instrumento opere dentro da precisão indicada pelo fabricante.
Mesmo os melhores componentes em seus equipamentos podem se alterar no decorrer do tempo, o que pode evidenciar que os resultados de medição não são mais tão precisos quanto no início. Por isso, é importante verificar regularmente se o equipamento ainda corresponde aos seus requisitos.
Através de uma calibração podemos constatar com maior precisão o estado do seu equipamento. Através disso é possível detectar e eliminar em tempo hábil possíveis erros de medição, antes que se tornem despercebidos e possivelmente resultem em resultados incorretos.
Portanto, a calibração ajuda a garantir que os seus equipamentos continuem a fornecer medições confiáveis e precisas, nas quais podemos confiar. Desse modo, você pode estar certo de que as suas medições sempre estão corretas e que você recebe os resultados desejados.
Recomendamos calibrar os equipamentos regularmente para assegurar que eles trabalhem com precisão e confiança. Contudo, não podemos apontar um intervalo de tempo fixo, no qual a calibração deve ser executada.
A frequência da calibração depende de vários fatores como, por exemplo, do seu sistema de gestão da qualidade, das condições específicas de utilização do seu equipamento e das suas características de desempenho. Às vezes é apropriado calibrar com maior frequência aplicações sensíveis que requerem uma maior precisão, enquanto que em outros casos, possa ser possível aumentar os intervalos de calibração, desde que os seus requisitos específicos o permitam.
Uma boa diretriz para a primeira calibração é observar as instruções do fabricante para o equipamento. Estas oferecem um bom ponto de partida e podem lhe ajudar a determinar o intervalo de calibração ideal para a sua situação específica.
Se você estiver inseguro ou necessitar de mais informações, você pode entrar em contato conosco ou dirigir-se ao fabricante do equipamento, para encontrar o melhor modo de procedimento. Assim, você pode assegurar que os seus equipamentos sempre estão em ótimo estado e que fornecem resultados confiáveis.
No nosso certificado de calibração você encontra todas as informações importantes sobre a calibração. Além dos valores medidos, isso inclui informações sobre a identificação inequívoca do objeto de teste (seu equipamento), as condições ambientais e o responsável pelo teste são mencionadas. Além disso, são referidas informações que são necessárias para o rastreabilidade, bem como as referências utilizadas e os processos utilizados.
A rastreabilidade é de máxima importância para assegurar medições exatas e confiáveis. Trata-se de um processo de comparação contínuo e documentado que integra a medição de um instrumento com um padrão nacional e legal reconhecido.
Para atingir uma calibração rastreável devemos calibrar corretamente cada instrumento e cada padrão em uma sequência hierárquica, que remonta até o padrão nacional, onde documentamos cuidadosamente os resultados.
A documentação serve como comprovação de que todas as calibrações na cadeia foram realizadas corretamente, e ela fornece as informações necessárias para comprovar o cumprimento. Em cada passo da cadeia de rastreabilidade calculamos e anotamos a incerteza de medição, para determinar uma incerteza global para toda a cadeia.
Laboratórios como o nosso, que contribuem para a cadeia de rastreabilidade, mostram a sua competência técnica através da acreditação e, com isso, fornecem a comprovação dos seus conhecimentos técnicos. A rastreabilidade exerce um papel decisivo no cumprimento de requisitos globais de medição e regulatórios. Ela confirma que os seus instrumentos fornecem medições em unidades aceitas com o nível de precisão acordado. Através do cumprimento de padrões de rastreabilidade você pode confiar na fiabilidade e validade dos seus resultados de medição e atender as expectativas, que estão regulamentadas por normas e regulamentações internacionais.
Nós realizamos nossas calibrações exclusivamente em nosso laboratório acreditado, pois lá monitoramos e controlamos fatores ambientais como temperatura e umidade do ar. Os seus equipamentos devem ser enviados ao nosso laboratório em Sulz, para lá se estabilizarem e aclimatizarem por pelo menos 12 horas, antes de iniciarmos as calibrações.
Não existe uma resposta clara para isso. As seguintes perguntas podem lhe ajudar na avaliação:
- Quando o equipamento foi calibrado pela última vez?
- De quanto tempo é o intervalo de calibração?
Muitas vezes o fabricante do equipamento fornece informações sobre o intervalo de calibração recomendado. Recomenda-se verificar os dados do fabricante e orientar-se com base nestas diretrizes, para assegurar que o seu equipamento sempre forneça resultados precisos. Em princípio, recomendamos 1 ano como intervalo de calibração.
Sim, estamos planejando expandir o âmbito de acreditação. O respectivo âmbito atual você encontra na nossa página web.
Estamos empenhados em calibrar os seus equipamentos o mais rápido possível. De modo geral, almejamos um tempo de execução de, no máximo, duas semanas em nossa empresa. Além disso, devem ser considerados os tempos de envio.
Uma calibração acreditada e uma calibração de fábrica são dois tipos distintos de processo de calibração, que são aplicados em diferentes contextos. A diferença principal entre eles está no tipo da certificação e rastreabilidade dos resultados de medição.
Realizamos a calibração acreditada em nosso centro de calibração acreditado, que está certificado pelo órgão de acreditação austríaco Akkreditierung Austria. A acreditação confirma que cumprimos determinados padrões de qualidade e que possuímos a competência de realizar a calibração de determinadas grandezas de medição. Os métodos de medição adotados, a rastreabilidade dos resultados de medição a padrões nacionais e internacionais e a insegurança de calibração são rigorosamente monitorados e documentados.
Uma calibração de fábrica, também chamada de calibração do fabricante, normalmente ocorre antes que o equipamento deixe a BAUR e seja fornecido a você. A calibração de fábrica serve para assegurar que o equipamento corresponde aos requisitos de desempenho especificados, antes de chegar às suas mãos.
Normalmente uma calibração acreditada oferece uma maior confiabilidade e reconhecimento por órgãos de certificação independentes, enquanto que uma calibração de fábrica apresenta um monitoramento e certificação menos rigorosa.