FAQ
Vous trouverez ici la réponse
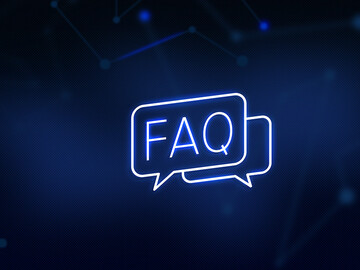
Bienvenue dans notre Foire aux questions où vous trouverez les réponses aux questions les plus fréquemment posées.
Nous savons qu’il peut parfois être difficile de trouver rapidement et facilement l’information adéquate. C’est pourquoi nos experts Service ont créé cette FAQ pour vous aider à résoudre vos problèmes et à répondre à vos questions.
Nous espérons que vous y trouverez tout ce que vous cherchez. Mais si vous avez d’autres questions ou si vous avez besoin de plus d’informations, n’hésitez pas à nous contacter.
Essai d’huile diélectrique
Pour les installations en service, diverses méthodes d'essai sont disponibles pour évaluer l'état de l'huile isolante. Ces méthodes d'essai peuvent être divisées en deux catégories de base :
- Évaluation de l'état actuel et de l'adéquation de l'isolation dans les équipements électriques :
- mesure de la tension de claquage sous charge diélectrique
- Mesure du facteur de dissipation
- Analyse du vieillissement du système d'isolation :
- Détermination de la résistivité
- Expertise optique de la couleur et de l'apparence de l'huile isolante
L'essai de la tension de claquage permet d'évaluer la capacité d'isolation des liquides diélectriques. Les résultats d'essai vous permettent de détecter la présence d'un vieillissement de l'huile, par exemple en raison d'une teneur en eau trop élevée, d'impuretés ou d'une oxydation de l'huile.
Vous trouverez ici toutes les informations à ce sujet et les appareils BAUR avec lesquels vous pouvez effectuer cet essai.
Les entreprises suivantes devraient effectuer régulièrement un essai de la tension de claquage :
- entreprises énergétiques, particulièrement dans les sous-stations
- entreprises énergétiques, surtout dans les centrales
- entreprises ferroviaires utilisant des transformateurs haute tension pour les locomotives et les appareillages de commande
- laboratoires d’essais pour les analyses d’huile fournissant des prestations de service dans le domaine des essais
- fabricants de transformateurs et d’appareillages de commande effectuant des contrôles de qualité de l’huile
- entreprises du secteur pétrolier contrôlant les huiles neuves en cours de production
Aujourd’hui, cinq types différents de liquides diélectriques peuvent être testés. Ce sont les suivants :
- huile minérale
- hydrocarbures de poids moléculaire élevé (HMWH)
- liquides à base de silicone
- liquides à base d’esters synthétiques
- Liquides à base d’esters naturels (huile végétale)
Les normes IEC 60422 (directives pour la surveillance et la maintenance) et VDE 0370 (directives pour la surveillance et la maintenance) ainsi que certains fabricants d’huile diélectrique recommandent certains paramètres.
L'essai de tension de claquage diélectrique est une méthode relativement rapide et simple pour déterminer le degré de contamination de l'huile isolante. Ces contaminants sont généralement constitués d'eau, mais peuvent également inclure des particules conductrices, de la saleté, des dépôts, des particules isolantes et des sous-produits de l'oxydation et du vieillissement de l'huile. Pour les équipements en fonctionnement, l'essai de tension de claquage diélectrique est un moyen pratique et efficace de détecter l'humidité et d'autres contaminants dans l'huile avant qu'ils ne provoquent une défaillance catastrophique. Les connaissances acquises grâce à cet essai peuvent également servir d'aide :
- Prévision de la durée de vie restante d'un transformateur
- Sécurité opérationnelle accrue
- Prévention des incendies de système
- Maintenance de la fiabilité
Vous trouverez les instructions relatives à la surveillance de l’huile diélectrique dans des situations d’exploitation dans les normes IEC 60422 (directives pour la surveillance et la maintenance) et VDE 0370 (directives pour la surveillance et la maintenance). La distinction se fait sur la base du type de transformateur, de la puissance et de la charge. Ces normes vous donnent des lignes directrices pour déterminer la fréquence des tests qui devrait être raccourcie en cas de résultats défavorables ou de sollicitations particulièrement élevées.
Pour obtenir des résultats significatifs de l'essai d'huile diélectrique, il est essentiel que l'échantillon d'huile soit correctement prélevé par un personnel formé. Voici quelques conseils pour vous aider à prélever correctement un échantillon.
Les caractéristiques individuelles de l'huile isolante peuvent également être présentées, dans une certaine mesure, par d'autres huiles. Toutefois, la particularité réside dans la combinaison de ces propriétés. Par exemple, d'autres huiles à faible viscosité peuvent avoir une tension de claquage élevée et éventuellement une résistance élevée et un faible facteur de perte diélectrique, à condition qu'elles soient propres et sèches. Mais ces propriétés peuvent changer lorsque le point d'écoulement est bas, le point d'éclair élevé et l'excellente résistance à l'oxydation entrent en jeu.
Il convient de noter que les huiles isolantes conventionnelles présentent cette combinaison de propriétés sans nécessiter d'additifs. Ceci est particulièrement important pour la réutilisation, car cela les rend idéales pour le recyclage.
Localisation des défauts de câble
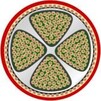
Blindé/Multifil
- Basse tension
- 3 ou 4 phases
- Blindage
- La plupart des défauts se produisent entre phases
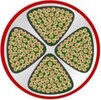
Non blindé/Multifil
- Basse tension
- 3 à 5 phases
- Défaut entre phase-terre et phase-phase
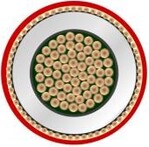
Blindé/coaxial
- Moyenne ou haute tension
- 1 phase
- 1 blindage
- Défaut entre phase et blindage
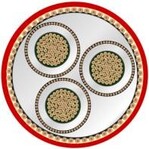
Blindé/coaxial
- Moyenne ou haute tension
- 3 phases
- 3 blindages
- Défaut entre phase et blindage
- Les défauts entre phases sont peu probables
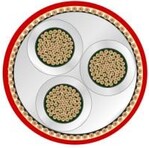
Blindé/coaxial
- Moyenne tension
- 3 phases
- Défaut entre phases ou entre phase et blindage
- La localisation des défauts est souvent difficile
En général, il existe 2 types de matériaux isolants pour les câbles d’énergie :
- l’isolation au papier, imprégnation dans la masse (PILC)
- le polyéthylène réticulé (XLPE)
Court-circuit
Des isolations endommagées conduisent à une connexion à faible résistance de deux conducteurs ou plus à l'emplacement du défaut.
Court-cirtcuit à la terre
Les défauts à la terre ou courts-circuits à la terre sont des liaisons à la terre présentant une faible résistance. Un autre type de défaut est la double mise à la terre qui présente deux courts-circuits à la terre espacés l'un de l'autre sur des conducteurs différents.
Défauts de gaine
Les dommages de la gaine extérieure du câble n'entraînent pas toujours des pannes franches. Ils peuvent toutefois générer à long terme des défauts de câble, notamment à la suite de la pénétration d'humidité et du fait de défauts d'isolation.
Défauts intermittents
Il arrive fréquemment que les défauts ne surviennent pas en continu, mais uniquement de temps en temps et en fonction de la charge appliquée au câble. L'une des raisons expliquant ce phénomène est l'assèchement des câbles isolés à l'huile en cas de faible charge. Une autre raison est la présence de décharge partielle due au vieillissement ou à des « arborescences électriques » dans des câbles.
Ruptures de câble
Des dommages mécaniques et des mouvements de terrain peuvent entraîner la rupture d'un ou plusieurs conducteurs.
La méthode d’échométrie basse tension (également appelée TDR) sert à localiser les défauts à basse résistance, les interruptions de câble ainsi qu’à déterminer la longueur des câbles. Vous pouvez en savoir plus ici.
-
Méthode d’échométrie basse tension (TDR) pour défauts à basse résistance et interruptions de câble
-
Méthode de réflexion sur arc multiple (MIS/MIM) pour la localisation des défauts à haute résistance et des défauts éclateurs
-
DC-MIS/MIM pour des défauts intermittents
-
Conditionnement du défaut MIS/MIM pour défauts de câble humides et difficiles à localiser
-
Méthode impulsion HT pour défauts éclateurs à haute tension
-
Méthode directe en choc pour défauts à haute résistance et défauts éclateurs
-
Méthode directe en tension pour défauts éclateurs chargeables
-
Mode de mesure avec représentation d’ensemble de courbes pour les petits défauts intermittents
-
Conditionnement de défauts (brûlage) pour défaut de câble à haute résistance sur câbles isolés à papier imprégné
Sur notre page d’applications, vous pouvez découvrir les détails sur les principales méthodes de mesure.
La réflexion sur arc multiple est la méthode la plus éprouvée et la plus précise pour la prélocalisation des défauts de câble. Les défauts à haute résistance et les défauts éclateurs sont amorcés par une seule impulsion HT. La distance au défaut est d’abord mesurée plusieurs fois et de manière très précise avec la technique TDR, puis analysée automatiquement.
Vous pouvez en savoir plus ici.
La méthode directe en choc vous permet de localiser les défauts à haute résistance et les défauts éclateurs. La distance au défaut est déterminée par l’analyse des diagrammes de chocs. Spécialement adaptée à l'utilisation sur les câbles de grande longueur. Vous trouverez tous les détails sur cette méthode de prélocalisation des défauts de câble sur notre page d’applications.
Dans la méthode DC-MIS/MIM, l’énergie est transmise directement dans le câble par le générateur de chocs, la décharge et l’arc électrique au niveau de l’emplacement du défaut ayant lieu lorsque le niveau de tension de sortie atteint le niveau de tension de claquage visé.
La méthode Impulsion HT sert à localiser les défauts éclateurs à haute tension. La détermination de la distance au défaut se fait par l'analyse automatique des ondes de réflexion oscillantes de la tension.
Vous trouverez tous les détails ici.
La méthode par pont de mesure sert à traiter les types de défaut suivants :
- défauts de câble à basse et haute résistance
- défauts de gaine à basse et haute résistance
- défauts de conducteur à conducteur dans les câbles non blindés
- défauts dans les câbles pilotes et les lignes de signaux
- défauts dans les conducteurs non blindés à la terre
La méthode acoustique sert à localiser l’emplacement exact des défauts à haute résistance et intermittents dans les câbles enterrés. Les impulsions émises par un générateur de chocs (SSG) font migrer une impulsion de tension le long du câble et les champs magnétiques et acoustiques sont détectés par le protrac®, notre localisateur de défauts de câble.
Le tracé de câble permet de trouver les types de défaut suivants :
- défauts à basse résistance sur câbles torsadés
- défauts sur câbles pilotes
- défauts sur câbles basse tension
- défauts sensible à la terre
- détection des liaisons câblées
Étalonnage
Notre accréditation restera effective et en vigueur tant que nous continuerons à respecter les normes et exigences de qualité élevées nécessaires à son attribution. Notre engagement en faveur de l'excellence et de l'amélioration continue nous permet de conserver notre accréditation et de continuer à vous offrir des prestations de service fiables et de qualité.
Notre accréditation témoigne de notre engagement en faveur des normes de qualité les plus élevées et de notre recherche constante de l'excellence. Avec ce label de qualité, nous voulons vous donner la certitude, en tant que client, que vous travaillez avec une entreprise professionnelle et digne de confiance.
Nous sommes convaincus que notre accréditation nous aide à travailler en permanence sur nos processus et nos méthodes de travail pour encore améliorer nos prestations de service et aller au-delà des attentes de nos clients.
Nous sommes accrédités pour les étalonnages des mesurandes de Courant et de Haute tension. Vous trouverez ici l’intégralité ce que couvre cette accréditation.
L’ajustement est un processus à part entière, différent de l’étalonnage. Alors que l’étalonnage détermine l’état actuel de l’appareil à tester sans y apporter de modification, l’ajustement se réfère à des adaptations ou des modifications permanentes de celui-ci pour le régler sur une norme ou une valeur de référence spécifique.
Notre processus d'étalonnage accrédité consiste simplement à effectuer des mesures qui vérifient la précision de l'unité testée et sa conformité aux normes spécifiées. Si un ajustement est nécessaire pour régler l’appareil à tester selon les spécifications requises, il est effectué en tant que processus à part entière, en dehors de l’étalonnage proprement dit.
Il peut cependant être effectué sur demande au cours d’un étalonnage accrédité ou réalisé en usine.
Découvrez ici l’ensemble du processus d’étalonnage accrédité.
L’étalonnage est un processus important au cours duquel sont comparés les mesures de votre appareil et celles d’un instrument de référence ou d’un étalon plus précis. Cela nous permet de détecter d’éventuelles erreurs dans l’appareil contrôlé. Dans certains cas, nous pouvons aussi l’ajuster pour corriger d’éventuels écarts. Cependant, un étalonnage réussi ne signifie pas automatiquement que l'appareil atteindra le niveau de performance spécifié. Il s’agit plutôt de s’assurer que l’instrument fonctionne dans les limites de précision indiquées par le fabricant.
Même les meilleurs composants de votre appareil peuvent subir des changements au fil du temps, ce qui pourrait rendre les résultats des mesures plus aussi précises qu'elles l'étaient auparavant. Il est donc important de régulièrement vérifier si l’appareil répond toujours à vos besoins.
Un étalonnage nous permet de déterminer son état exact. Cela permet d'identifier et de rectifier à temps toute erreur de mesure cachée, plutôt que de la laisser passer inaperçue et d'aboutir à des résultats potentiellement erronés.
L’étalonnage permet donc de vérifier que votre appareil continue à fournir des mesures fiables et précises sur lesquelles vous pouvez compter. Vous pouvez ainsi être sûr que vos mesures sont toujours correctes et que vous obtenez les résultats souhaités.
Nous recommandons de faire étalonner régulièrement les appareils pour garantir leur fonctionnement précis et fiable. Cependant, nous ne sommes pas en mesure de fournir un intervalle de temps spécifique pour l'étalonnage.
La fréquence de l'étalonnage dépend de divers facteurs, tels que votre système de gestion de la qualité, les conditions de fonctionnement spécifiques de votre appareil et vos caractéristiques de performance. Il est parfois opportun de faire étalonner plus souvent les applications sensibles qui nécessitent une plus grande précision, tandis que dans d'autres cas, il est possible d'allonger l'intervalle d'étalonnage si les besoins individuels le permettent.
Une bonne ligne directrice pour le premier étalonnage est de suivre les instructions données par le fabricant de l'appareil. Elles constituent un bon point de départ et peuvent vous aider à déterminer l'intervalle d'étalonnage optimal pour votre situation spécifique.
En cas de doute ou si vous avez besoin de plus d'informations, vous pouvez nous contacter ou contacter le fabricant de l'appareil afin de déterminer la meilleure façon de procéder. Ainsi vous aurez la certitude que vos appareils seront toujours en parfait état et qu'ils vous fourniront des résultats fiables.
Notre certificat d'étalonnage contient toutes les informations importantes relatives à celui-ci. Outre les valeurs mesurées, il comprend des informations sur l'identification unique de l'unité testée (votre appareil), les conditions environnementales et le contrôleur ayant effectué l'étalonnage. Il énumère également les informations nécessaires à la traçabilité, telles que les références et les procédés utilisés.
La traçabilité est d'une importance capitale pour garantir des mesures précises et fiables. Il s'agit d'un processus de comparaison continu et documenté associant la mesure d'un instrument à un étalon national et légal reconnu.
Pour qu'un étalonnage soit traçable, nous devons étalonner correctement chaque instrument et chaque étalon dans une séquence hiérarchique remontant jusqu'à l'étalon national, en documentant soigneusement les résultats.
La documentation sert à prouver que tous les étalonnages de la chaîne ont été effectués correctement et fournit les informations nécessaires pour démontrer la conformité. A chaque étape de la chaîne de traçabilité, nous calculons et notons l'incertitude de mesure afin de déterminer un degré d'incertitude total pour l'ensemble de la chaîne.
Les laboratoires tels que le nôtre qui contribuent à la chaîne de traçabilité démontrent leur compétence technique par le biais de l'accréditation, apportant ainsi la preuve de leurs connaissances spécialisées. La traçabilité joue un rôle essentiel dans le respect des exigences mondiales en matière de mesure et de réglementation. Elle confirme que vos instruments fournissent des mesures dans les unités acceptées avec les niveaux de précision convenus. En respectant les normes de traçabilité, vous pouvez être sûr de la fiabilité et de la validité de vos résultats et satisfaire ainsi les attentes fixées par les normes et prescriptions internationales.
Nous n'effectuons nos étalonnages que dans notre laboratoire accrédité, car c'est là que nous sommes en mesure de surveiller et de contrôler les facteurs environnementaux tels que la température et l'humidité. Vos appareils doivent être envoyés à notre laboratoire de Sulz afin de se stabiliser et de s’adapter à notre environnement pendant au moins 12 heures avant que nous ne commencions les étalonnages.
Il n'y a aucune réponse claire à ce sujet. Les questions suivantes peuvent vous aider à estimer la situation :
- de quand date le dernier étalonnage de votre appareil ?
- à quelle fréquence effectuez-vous l’étalonnage ?
Le fabricant de l’appareil fournit régulièrement des informations sur la fréquence d’étalonnage conseillée. Il est conseillé de vérifier les indications du fabricant et de se référer à ces directives pour s’assurer que votre appareil fournit toujours des résultats précis. En principe, nous recommandons un intervalle d’étalonnage d'un an.
Oui, nous avons l’intention d'étendre la portée de l'accréditation. Vous trouverez la portée actuelle de l’accréditation sur notre site internet.
Nous nous efforçons d’étalonner vos appareils le plus rapidement possible. En règle générale, nous partons sur un délai d’exécution dans nos locaux de deux semaines maximum. Tenez également compte des délais d'expédition.
Un étalonnage accrédité et un étalonnage en usine sont deux types de procédures d'étalonnage différents, utilisés dans des contextes différents. La principale différence réside dans le type de certification et la traçabilité des résultats de mesure.
Nous réalisons l’étalonnage accrédité dans notre centre d’étalonnage accrédité certifié par l'Akkreditierung Austria. L’accréditation confirme que nous répondons à certaines normes de qualité et que nous avons les compétences pour réaliser l’étalonnage de certaines mesurandes. Les méthodes de mesure utilisées, la traçabilité des résultats de mesure par rapport aux normes nationales ou internationales et l'incertitude d’étalonnage sont strictement contrôlées et documentées.
Un étalonnage en usine, également appelé étalonnage du fabricant, est généralement effectué avant que l’appareil ne quitte les locaux de BAUR et ne vous soit livré. L’étalonnage en usine sert à s’assurer que l’appareil satisfait les exigences de performance spécifiées avant qu’il ne vous parvienne.
Un étalonnage accrédité offre généralement une plus grande fiabilité et la reconnaissance par des organismes de certification indépendants, tandis qu’un étalonnage en usine présente une surveillance et une certification moins strictes.