Sheath testing with BAUR
Sheath fault location is essential for preventing cable damage and failures. The maintenance process of a cable network involves detecting, locating, and rectifying cable sheath faults early in order to prevent the worst-case scenario from happening. This is firstly achieved by sheath testing, then fault pre-location using the Murray and Glaser bridge methods and subsequent cable sheath fault pin-pointing. These procedures are supported by the BAUR shirla automatic sheath test and fault location device.
Detecting cable sheath faults by testing
Damage to the outer sheath of cables is a common cause of cable faults. This damage almost always leads to water penetration, thus reducing the quality of the insulating material over time until it is completely destroyed.
In MV and HV cables, in particular, such sheath defects also aid the growth of water trees, which again lead to the failure of the cable. In the context of diagnostic condition maintenance, it is essential that cable sheath faults are rectified, as expensive diagnostics is relatively pointless if weak points caused by sheath faults can continue to grow.
In sheath testing, a test voltage of up to 10 kV is applied to the cable screen over a period of at least one minute whilst the leakage current to earth is measured. It is important that the cable screen is disconnected from the earthing at both ends during the entire measurement, as otherwise the test current would take the route direct to earth, short-circuiting the actual fault. The leakage currents measured will differ depending upon the outer sheath material, the degree of ageing in this sheath, the length of the cable and the number of joints. A certain amount of knowledge of the cable and experience is therefore required. If the leakage current moves from the µA range into the mA range, or increases suddenly, e.g. during testing, this is a sign of a potential problem.
Sheath fault pre-location
If an elevated leakage current, indicating a cable sheath fault, is detected during testing the fault should be rectified as quickly as possible. The reflection measurement technique is unsuitable for locating cable sheath faults or faults due to earth contact, as the ground does not represent a usable return phase in such fault types.
Bridge measurement methods are particularly appropriate for the pre-location of cable sheath faults. They are based on the ratio method in which the resistance is determined before and after the fault location. This pre-location is performed by applying DC voltage to a cable route that has been disconnected from the network.
The BAUR shirla allows bridge measurements to be performed according to the Murray or Glaser principle. Both principles are based on the Wheatstone bridge circuit, in which the two points in the measuring circuit are balanced to the same potential so that a measuring unit (previously a galvanometer) connected between these points does not display any current. The bridge circuit is then in equilibrium.
The measurements themselves are performed fully automatically by the BAUR shirla. The operator needs only enter the maximum voltage, length, material and cross-sections of known sections and connect the test cables to the test object. After the measurement has been completed, the fault distance is shown on the display.
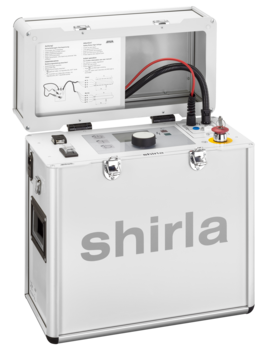
shirla
Portable device for sheath testing
Cable sheath fault pin-pointing
The pre-location described above determines the distance from the fault. However, since an underground cable is never straight, the fault position is only ever known approximately. Even with a measuring pre-location accuracy of 0.1% and above, the difference that can be expected from the actual geographic position is up to ±10%. For a 1 km long cable, this could represent a possible fault position within a range of 200 m.
Pin-pointing serves to eliminate this lack of accuracy using measuring technology, and to reduce the amount of excavation work required to a minimum. To this end, a pulsed DC voltage is fed into the faulty screen and the voltage then measured on site with a special voltmeter using earth spikes as measuring electrodes. The pulsing improves recognition of the signal, but also eliminates faults due to galvanic effects or other voltages in the ground.
Among other things, the protrac® pin-pointing system is used for the precise pin-pointing of cable and cable sheath faults. Thanks to the use of the latest technologies, locating the exact fault position with the protrac® is extremely fast and precise. The innovative two-level signal processing concept permits a high degree of sensitivity and accuracy, and maximum suppression of ambient noise.
When pin-pointing with the protrac®, the step voltage probes (SVP) are used in conjunction with the CU control unit and an HV source to locate cable sheath faults.
The principle of pin-pointing is simple: the deflection of the voltmeter points towards the fault and the measured voltage increases steadily as the fault is approached. Shortly before the fault location is reached the voltage rises sharply and then falls to zero as soon as the earth spikes are inserted symmetrically to either side of the fault. The precise position of the cable sheath fault is thus located.
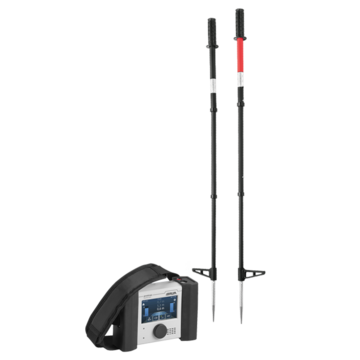
protrac® step voltage set
Sheath fault location with step voltage
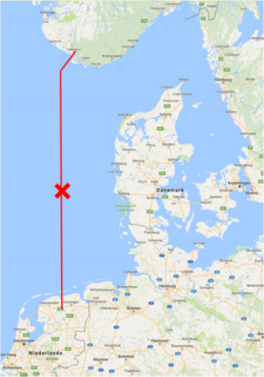
Case study of an HVDC cable
Sheath fault location with a measuring bridge is suitable for a diverse range of cables. It is even possible to measure cables hundreds of kilometres long, which is what took place on the 450 kV HVDC connection between Norway and the Netherlands.
A cable sheath fault was successfully located on the 580 km long cable route using a BAUR device and the Murray bridge measurement method.
The cable sheath fault was measured approximately level with Esbjerg. The relatively accurate pre-location of the fault along the 580 km long submarine cable simplified and sped up the fault pin-pointing process.